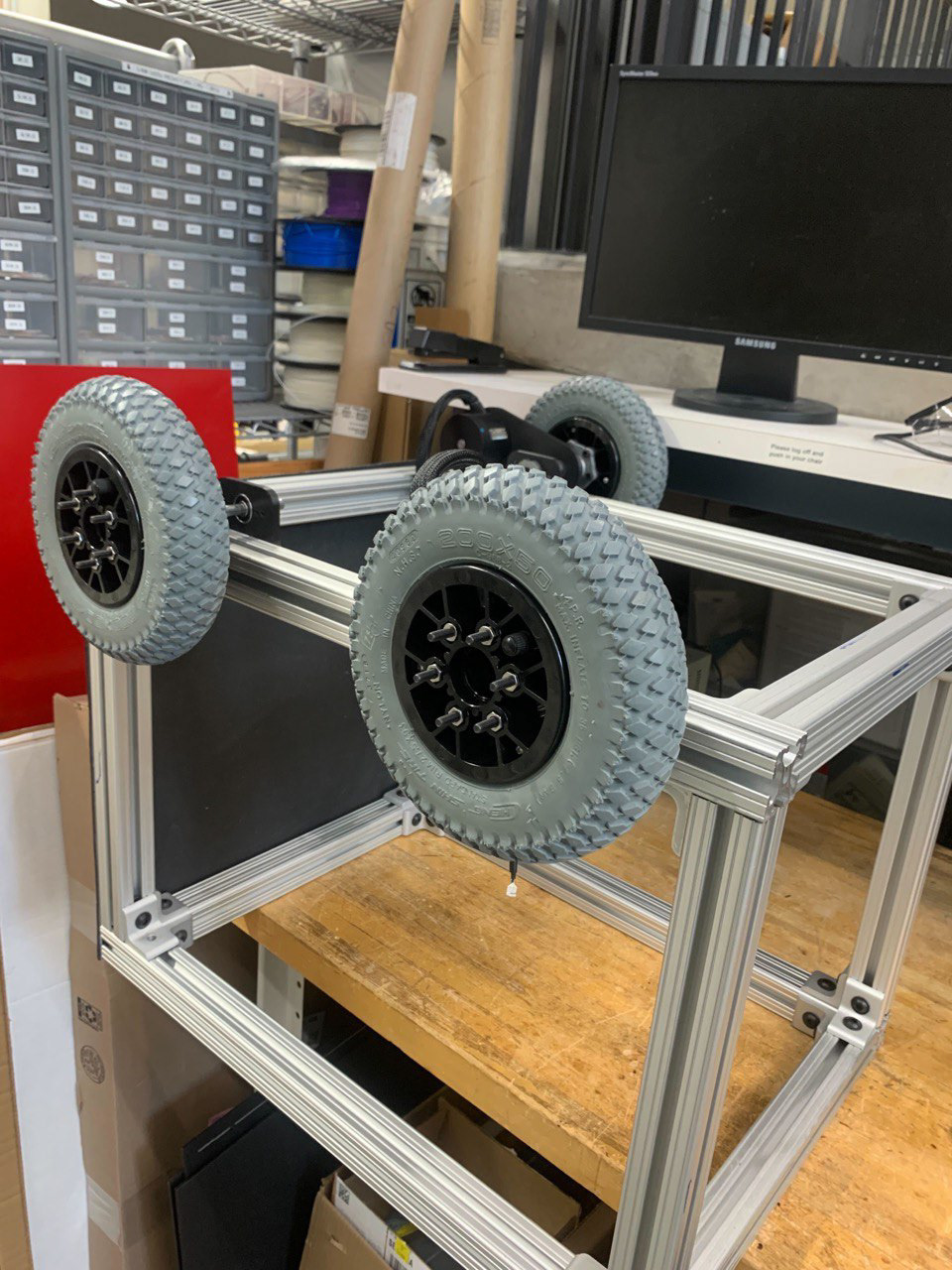
I designed and selected parts for the development of the drivetrain in collaboration with a teammate. The robot is a four-wheel drive vehicle with the motors mounted parallel to the wheels' shafts. The motor power is translated through two motor pulleys in a 1:1 ratio, as the motors themselves were already over-spec for the initial goal of the project, which was to move the robot forward on a fifteen-degree incline plane. There was a safety factor of 11 between the force required to achieve this goal and the maximum force that the motors could output, considering our power system.
I manufactured and assembled mounting parts using 3D-printed composite structures, specifically utilizing polycarbonate carbon fiber filament for lightweight yet strong mounting components. The frame was constructed with 80-20 for easy access and quick prototyping.
Additionally, I worked closely with the electronics and software team to integrate sensors into the structure and shield the electronics within the system. Special attention was given to securely mounting the batteries.
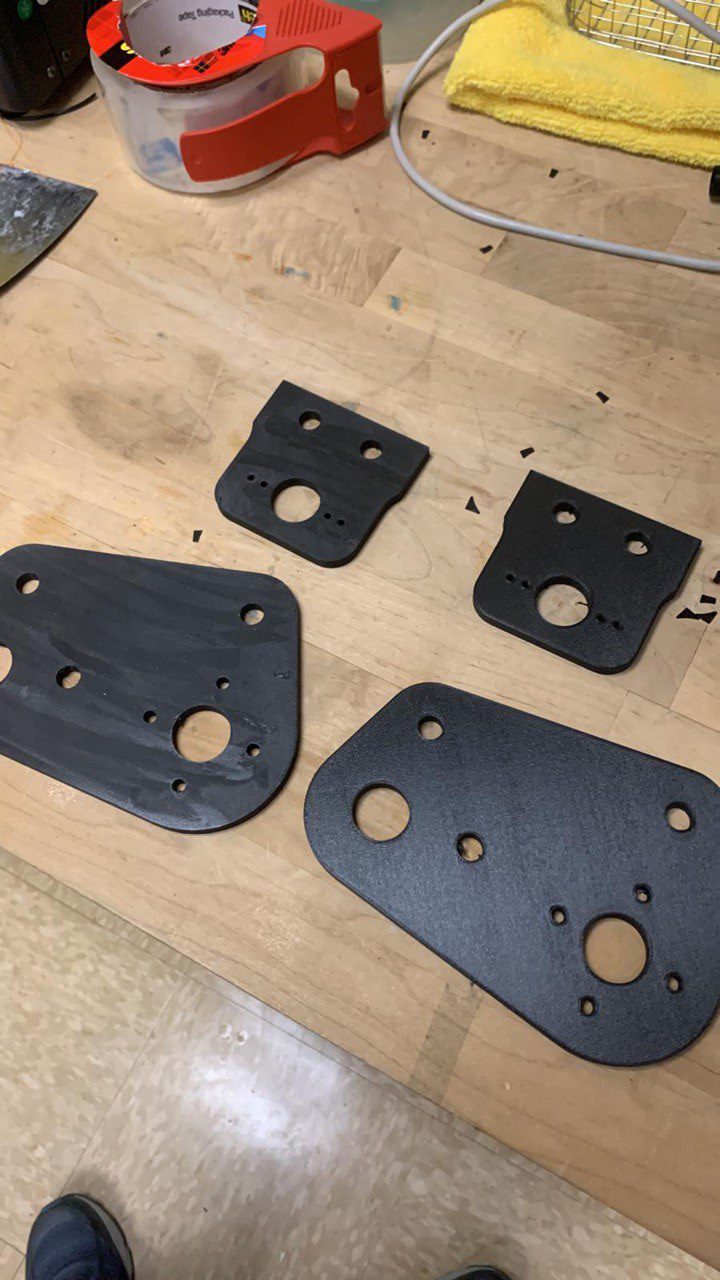
Demonstration of the Performance of our First Prototype