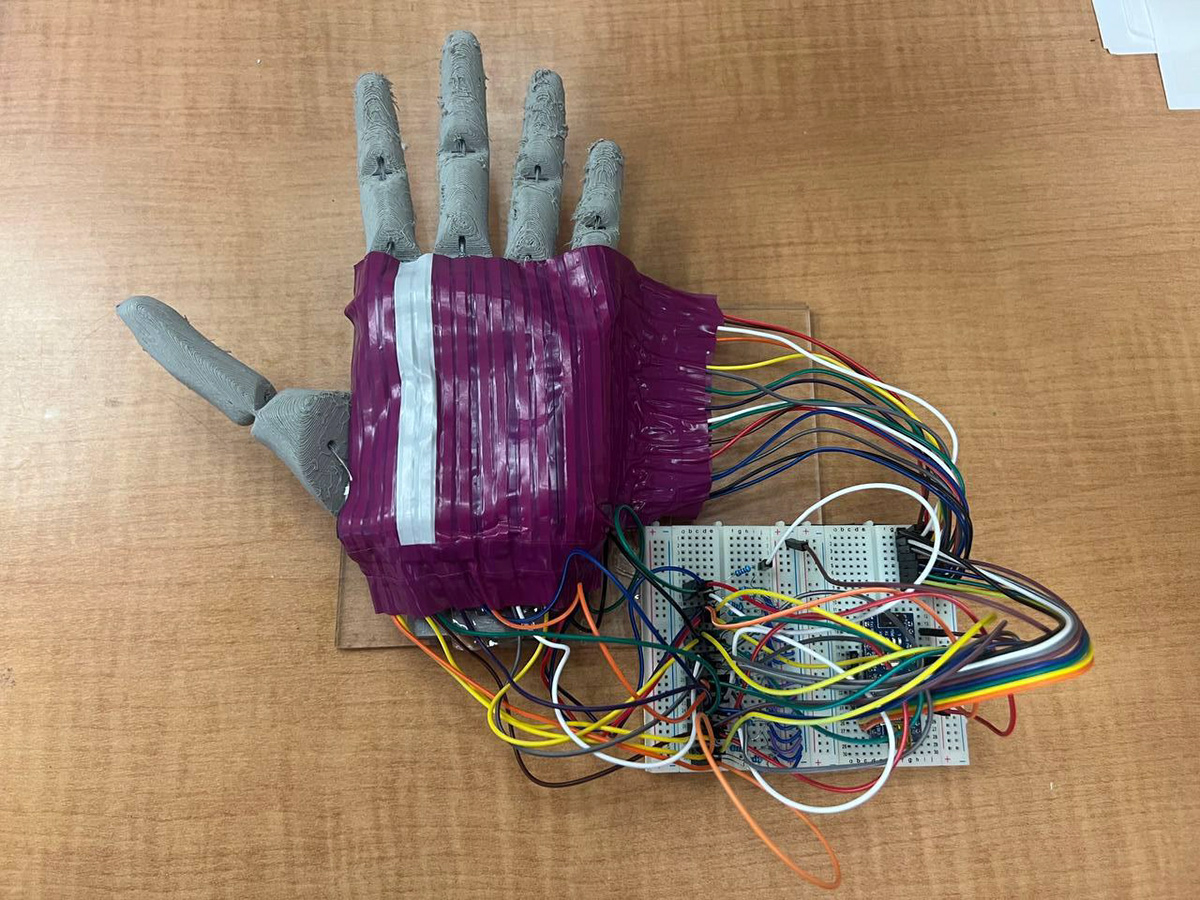
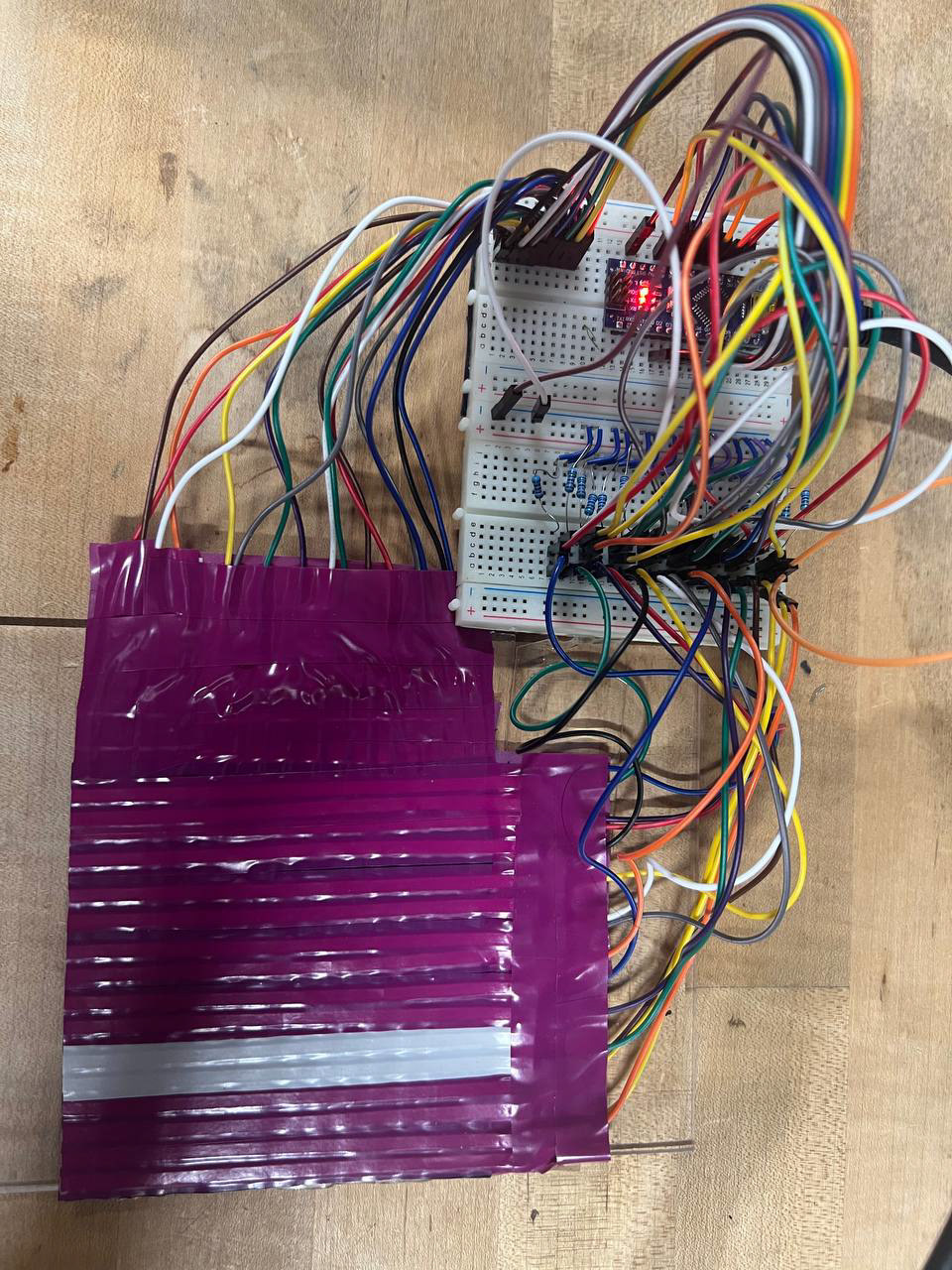
I developed molds and manufacturing processes to increase reliability and reduce internal stresses on the sensors. The sensor consists of a piezoresistive material and multiple copper lanes that run orthogonally to each other and at their interception creates a resistance change if a force is present.
I created custom high-density low latency flexible force sensors with 256 sensing points, which are processed in a Wheatstone bridge, rendered on an Arduino Nano. This data is later displayed by a front-end GUI created in Processing.
The sensors' ability to work on nonuniform surfaces provides an opportunity to be integrated into prosthetics hands, UR5's grippers, and other robotic applications where force sensing can provide information to the low-level controller for a more accurate interaction.
This work was recorded in the paper titled " Enhanced Embedded Force Sensing in Sensorized Prosthetic Hands with Multilayered Piezoresistive Arrays" which was accepted for publication at the 2023 World Haptics Conference.
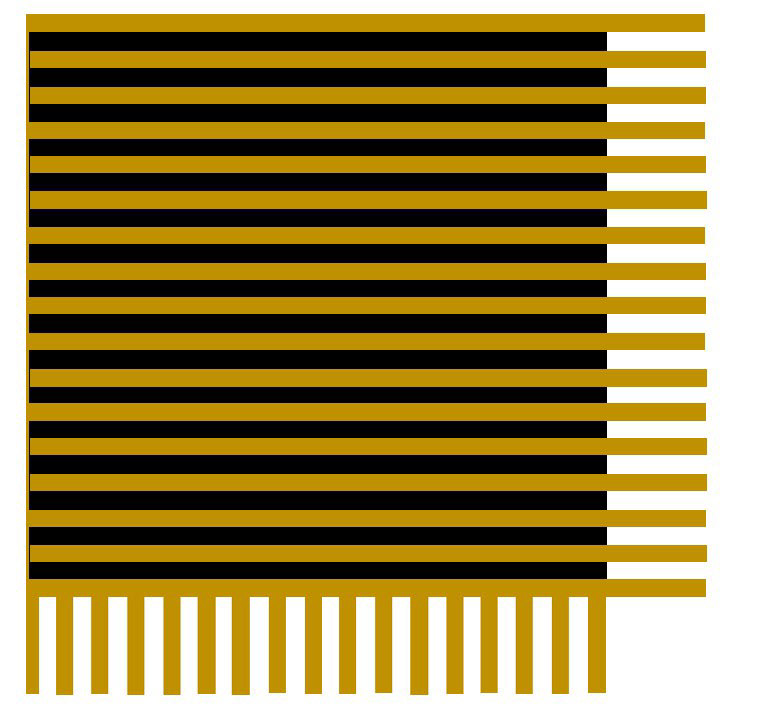
Demonstration of the Performance of the Second Iteration of Piezoresistive Force Sensor