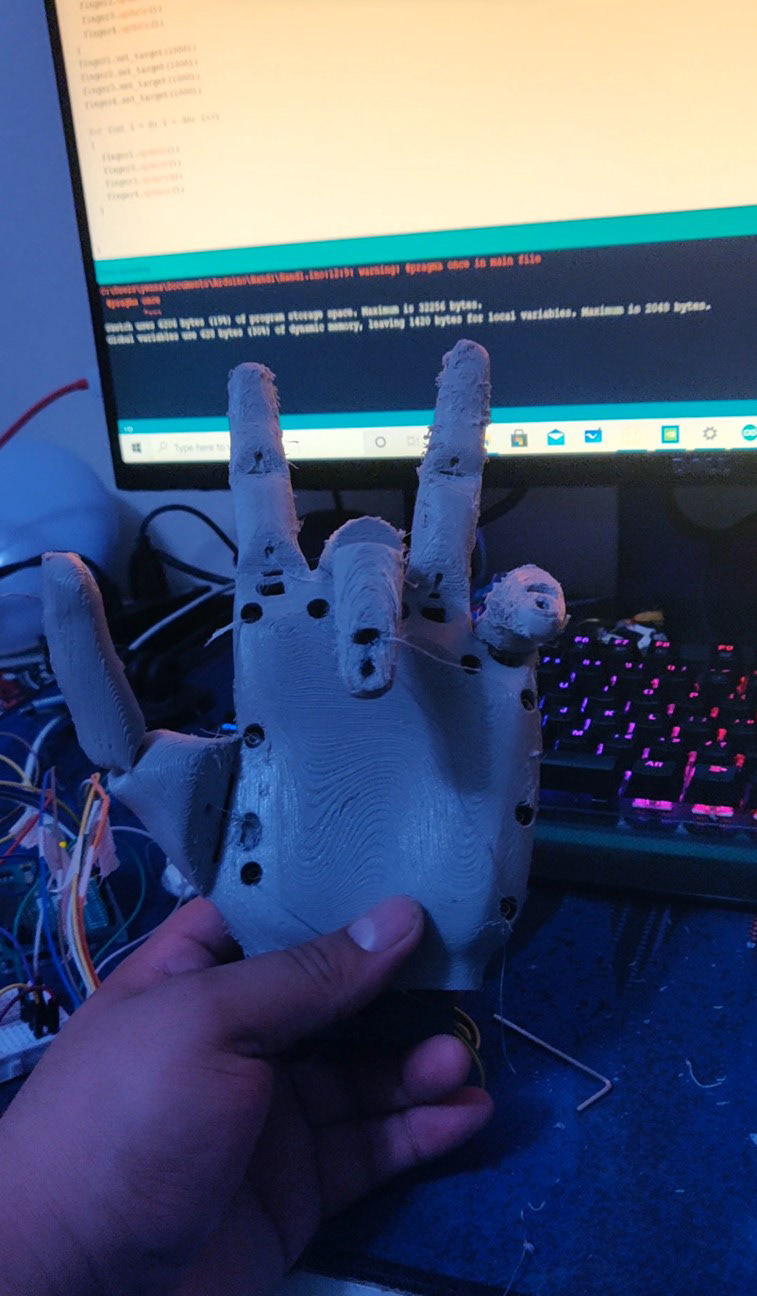
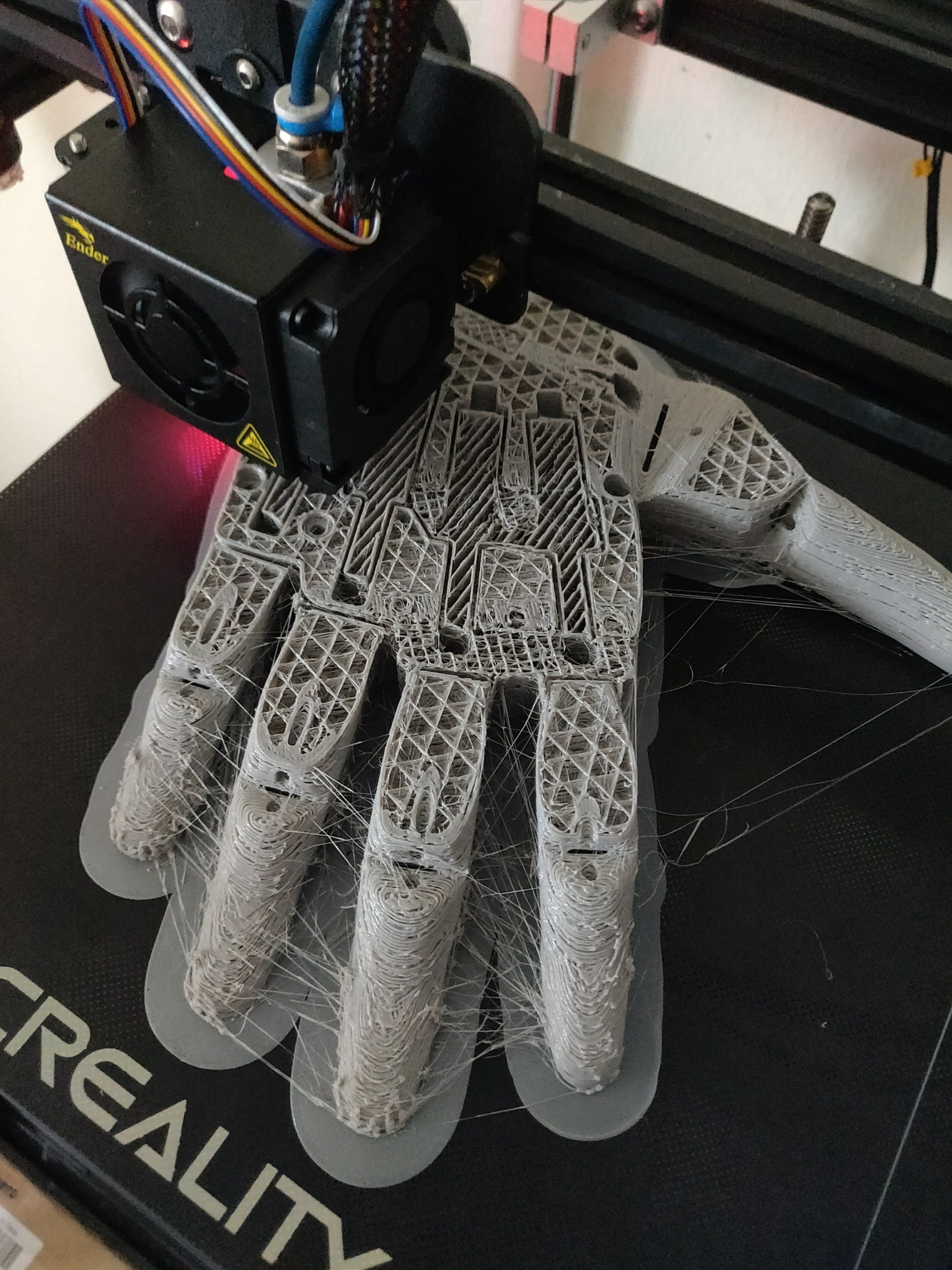
I identified a cost and supply issue with components for open-source prosthetic hands and decided to focus on the Open Bionics ADA hand. Many of the components needed to build and operate the original system had been phased out.
Given this issue, I decided to re-engineer a prosthetic hand designed by Open Bionics to suit the cost and availability of parts.
I crafted a functional prototype through modular coding, utilizing micro linear actuators, an Arduino Nano, and innovative 3D-printed parts. The hand operates by using the elastic properties of TPU and a series of heavy-duty fishing lines, which are pulled by the linear actuators, causing the fingers to flex. When the linear actuators are turned off, the elastic nature of the TPU returns the hand to its original position. The position of each finger can be controlled by manipulating the position of the corresponding linear actuator relative to its starting point.
The prosthetic hand demonstrated excellent performance, with low power consumption in a compact setup that included an Arduino Nano and two motor drives. The system used a 12 Volt/5A power supply, which can easily be replaced with a lithium battery, or in the future, a solid-state battery.

Demonstration of the Performance of the Second Iteration Open Source Prosthetic Hand
Demonstration of the Performance of Linear Actuators